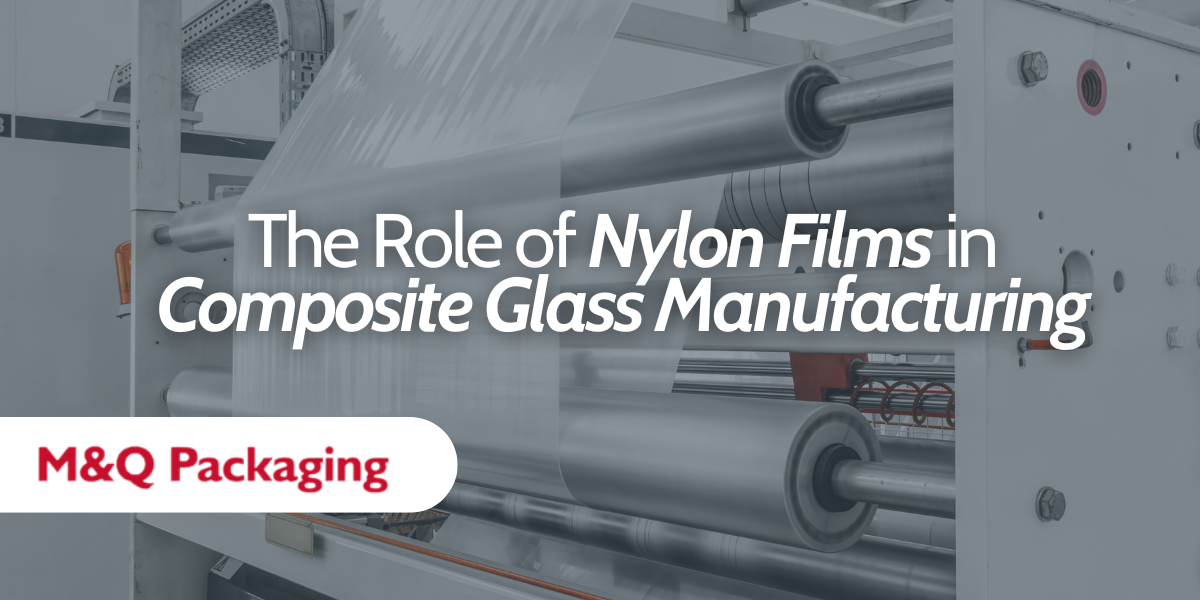
Introduction
Composite glass—a layered material combining glass sheets with adhesives or polymers—is critical in industries demanding exceptional strength and durability. From ballistic-resistant windows to aircraft canopies, its structural integrity relies on precise manufacturing processes. Vacuum bagging films play a pivotal role by applying uniform pressure during high-temperature curing, ensuring layers bond flawlessly without influencing thermal warping.
M&Q’s exclusive nylon vacuum bagging films stand out in this niche, offering unmatched heat resistance (up to 400°F) and adhesion consistency. Engineered to endure extreme conditions, these films outperform traditional materials, delivering durability, chemical resistance, and thermal stability trusted across sectors like aerospace, automotive, and defense.
How Nylon Vacuum Bagging Films Enhance Composite Glass Production
- Ensuring Optimal Adhesion
Composite glass requires layers of glass and adhesives to fuse seamlessly under consistent pressure. M&Q’s nylon films are specifically designed for vacuum bagging, eliminating air pockets and ensuring defect-free adhesion. This process is vital for applications like ballistic glass, where layer integrity is non-negotiable. Notably, while the films facilitate bonding, they do not impact the thermal warping properties of the glass itself. - Withstanding Extreme Heat
High-temperature ovens (up to 400°F) are standard in composite glass curing. M&Q’s 100% nylon films retain structural integrity under these conditions, enabling reliable performance without degradation. Their heat resistance ensures consistent pressure application, critical for aerospace cockpit windows and windshields. - Safeguarding Material Integrity
Maintaining vacuum integrity is essential in composite glass manufacturing. M&Q’s puncture-resistant nylon films prevent holes or tears that could compromise the vacuum seal, ensuring consistent pressure throughout the curing process. Their chemical resistance also helps prevent interference with adhesives, supporting flawless bonding and structural clarity. This dual protection is essential for automotive windshield manufacturing, where clarity and durability are paramount.
Applications Across Industries
- Ballistic Glass: M&Q’s films ensure precise layering for impact-resistant military and security installations, leveraging superior tensile strength and thermal resistance.
- Aerospace Glass: Withstand cockpit window curing at extreme temperatures, meeting rigorous safety standards outlined in aerospace packaging solutions.
- Windshield Glass: Prevent contamination, ensuring distortion-free automotive glass with enhanced impact resistance.
- Safety Glass: Produce shatter-resistant panels for architectural use through reliable vacuum bagging.
Why M&Q Nylon Films Lead the Industry
M&Q’s leadership in the industry stems from its exclusive focus on 100% nylon films, which inherently offer superior strength and heat resistance compared to generic alternatives. With over seven decades of expertise in industrial film innovation, the company has refined solutions for high-stakes manufacturing environments. Customization is central to M&Q’s approach—films are available in varying thicknesses, widths, and formats to align with unique production requirements. Every film is proudly manufactured in the USA under stringent quality controls, guaranteeing repeatable performance and adherence to the highest industry benchmarks.
Conclusion
M&Q’s nylon vacuum bagging films are indispensable for composite glass manufacturing, offering thermal resilience, adhesion consistency, and material protection—without affecting thermal warping properties. Their success in aerospace, automotive, and defense underscores their adaptability to rigorous industrial demands.
Upgrade Your Manufacturing Process
Discover how M&Q’s specialized nylon films can optimize your composite glass production. Contact our team today for tailored solutions or material specifications.